This is one of two articles that focused on getting the most out of your building automation system. In this article, we will share some suggestions on using warnings to monitor system conditions. By taking some time to set up warnings on control points, you can use real-time building automation system information to identify which piece of equipment requires the attention of building operators before the issues turn into occupant complaints.
Alarms are a very common part of any automation system. They are used to tell building operators when things are too hot, too cold, when the command of an object does not match the status of the object, and many other conditions. What alarms will not do is allow operators to see when things are not properly controlling before they get outside of the allowable operating parameters. Setting up warnings on control points fills this gap.
Warnings are best used on analog outputs like damper commands, valve commands, pumps and fan speed outputs, as well as, PID loop values like cooling demands, heating demands, or static pressure resets. Warnings do not work for two-position equipment that require the control device to be on or off, nor will it work for equipment in series where one device is supposed to completely open before a second device starts to open. One example of this could be a 1/3 valve 2/3 valve operation.
Warnings can be setup in many ways but one common way is to add a warning to a point that is at 100% of its control range. In an effort to maintain control, the point has gone to its extreme position and is, or will likely soon be, letting the control variable drift out of the correct range. Examples of this would be a radiation valve that is 100% open but the room temperature continues to drop or a VAV-box that is providing 100% of the design air flow but the temperature is still increasing in the space. Figure 1 shows a VAV box that is 100% open but is shy of its design air flow by 30%.
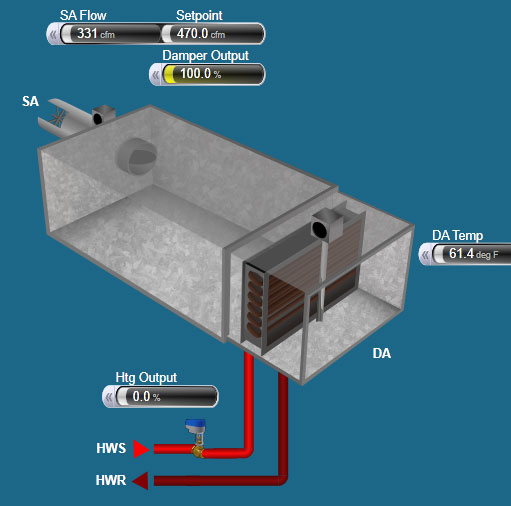
Figure 1: VAV with reduced airflow
Johnson Controls, Metasys® Building Automation System, screen capture from District Energy’s Jemne office
Catching issues like this will help to prevent uncomfortable indoor conditions and reduce excess energy usage before they become major failures. In this reduced air flow example, the issue could be related to a reheat coil that has become coated with dust and debris and is no longer allowing enough air through the coil or it could be play or slack in the damper linkage. Regardless of the issue, a physical examination of the equipment is the only way to determine the problem.
Setting up warnings on your building automation system is another tool that building operators can use to monitor and manage building equipment. In the first article, we shared some suggestions on using totalizers to verify equipment run time and using pressure independent valves to monitor energy.
If you have questions about energy savings opportunities or your District Energy connection, please contact our team at 651.297.8955, email info@districtenergy.com, or support request form.